What is a 3D printer?
A 3D printer is a tool that is able to produce a 3D object from a CAD file by stacking layers of material, sintering powders or hardening resins. There is different commercial and OpenSource softwares that are used for Computer Assisted Design (Dassault System CATIA, Solidworks, Autodesk Maya, 3DsMax, AutoCAD, ZBrush, Blender). Anyway the produced file must be reinterpreted by the printer's software to get a machine process.
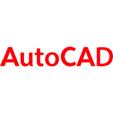

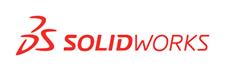
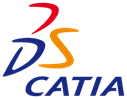
How to use it?
Few decades ago the only way to describe your design and make it understandable to everyone was draw to 2D blueprints on paper. Now we use 3D modeling software. With modern computer’s calculation power the user see his model on his screen in real time and modify it instantaneously. Then it is possible to send it to someone else or print blueprints from it. There is three main ways to obtain the 3D model:
- The first one is to draw it from scratch using toolboxes included in the software. With a computer, it is possible to apply the finite elements method to learn stress inside a component virtually saving times and money.
- The second is by using a 3D scanner.
- The third is downloading the file made by others from databases, specialized website or through the office network. This kind of scanner has the ability to transform a portion of its environment to numerical data. Then transform these points into a polygon model. It can be the road in the case of an unmanned car, or here an object, copying it.
Another way for simple geometries is to make algorithms to generate it but it's not the easiest way
The last part is translating the model to something understandable by the printer. In certain cases the operator must adapt the 3D model by adding support structure so unfinished parts of the model won't move during the printing process. Then transfer the instructions to the printer as a machining process. These softwares are developed by the manufacturer.
Softwares used to process 3D models
In our case, we use Catia for the design and the virtual assembly of each parts.
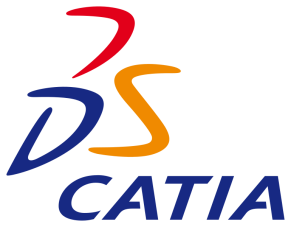
We use the software Makerbot Desktop to translate CATIA's CATPart to a file that can be processed by the 3D printers in Fablab. So in makerware, we need to put our different peaces in a good way.
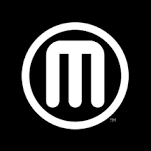
We use the Makerbot Replicator in the Fablab of Brussels. It’s a "low-cost" open-source 3D-printer based on plastic extrusion process. There are 3 versions of the printer available and 2 kinds of plastics.
Comparing printers: REPLICATOR 1, 2, 2X
There is three types of Replicators printers, each one with it's own characteristics. Replicator 1 was the only one available at the VUB, and given that it was the first model released, it was the less accurate between the three according to other groups.
Replicator 2 and 2X are almost the same model, the main difference is that the board on 2X is bigger, so it's possible to print extended models. Two printing head can be placed in the same machine but only one was set up. It is usefull if the user wants a bicolor product.
At the Fablab each model were available. We used one or another depending on which ones were free and what printing material was the most adapted to our project.
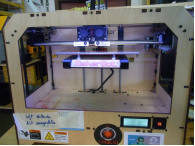
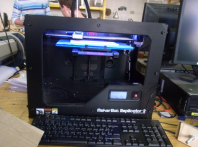
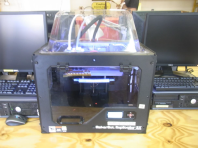
Fablab
We went to the fablab around 4 times. Fablab is open for everyone during 13h to 21h Wednesday. The problem is that there are a lot of people that want to use the 3D-printers. Often we couldn't use any of them and had to wait for another printing process to end. Print takes long time, from 2 hours to 3 hours for a simple a bit large part.
The Replicators printers are in the not so low end category of printers. We had issues while printing due to problems with the chosen technical solution by Makerbot. Some parts had to be print twice because it failed due to problems like the piece unsticking from the base or the plastic getting stucked in the printing head.
Plastic extrusion based process
Thermoplastic extrusion is an additive process. Most of the low cost printers uses this technology because ABS isn’t expensive and the working principles are easy to transform in a printer. Plastic extrusion 3D printer like the MakerBot cost about 2000€.
The available material available at the FABLAB are:
- ABS is one of the most used kinds of plastic that can be injected. It is affordable and sturdy.
- PLA as the advantage to be eco-friendly because it can be degraded easily in the nature. PLA is eye candy because of its transparent glow but it is a bit less sturdy than ABS.