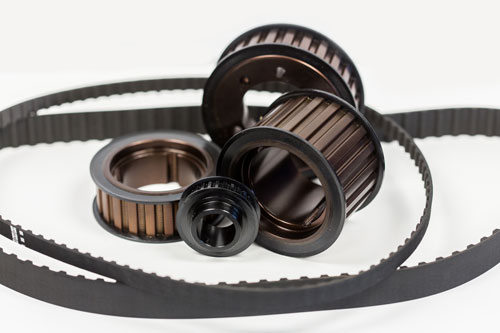
Belts & pulleys
During the 3D design the specifications from the egg-incubating company needed to be taken into account. The main idea was to build a gripper that could hold and release an egg using as less energy as possible. With this designed mechanism the opening and closing of the gripper requires energy but there is no need for current to keep the egg gripped.
The first idea for the up and down movement of the platform was using a rack and pinion mechanism. Due to cost and complexity the use of pulleys and belts was preferred. The main problem was here that the belts needed to be tensioned and thus a tension mechanism needed to be designed as well. Once the entire design was completed, the 3D printing and assembling part could start.
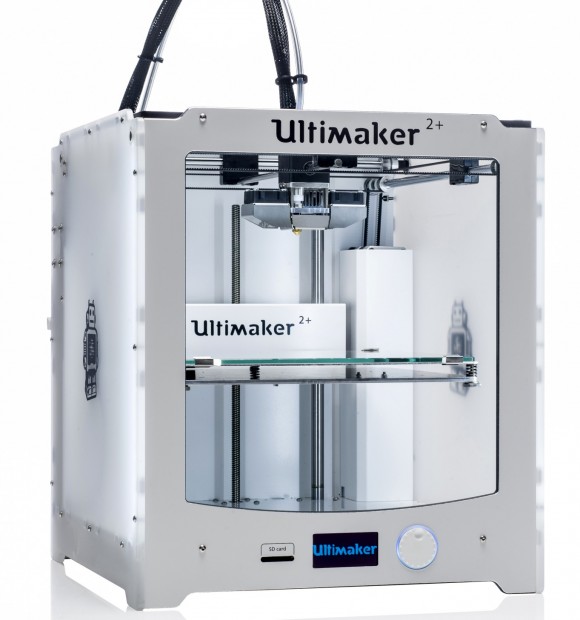
Tolerance on the precision
During the assembly of the 3D printed parts a few problems were encountered. Due to imperfections of the printer some holes were too small or even too big. Screwing through the parts would force the screw in but after some time wear occurred and the connections were loosening (even when threads were made). The tolerance on the position of holes (designed for assembling) was determined by the precision of the used printer, the Ultimaker 2+, and was much larger than expected (several millimeters).
Reprinting was avoided as much as possible for time and material considerations and thus in some cases glue was used for additional fixation in case the screw connection would fail. Due to these imperfections, asymmetries,etc friction and imbalance became more and more relevant. Drilling and filing managed to reach satisfying conditions but there was still some friction and imbalance in the structure (most of it between the head fixation for the stepper motor actuating the pulleys).
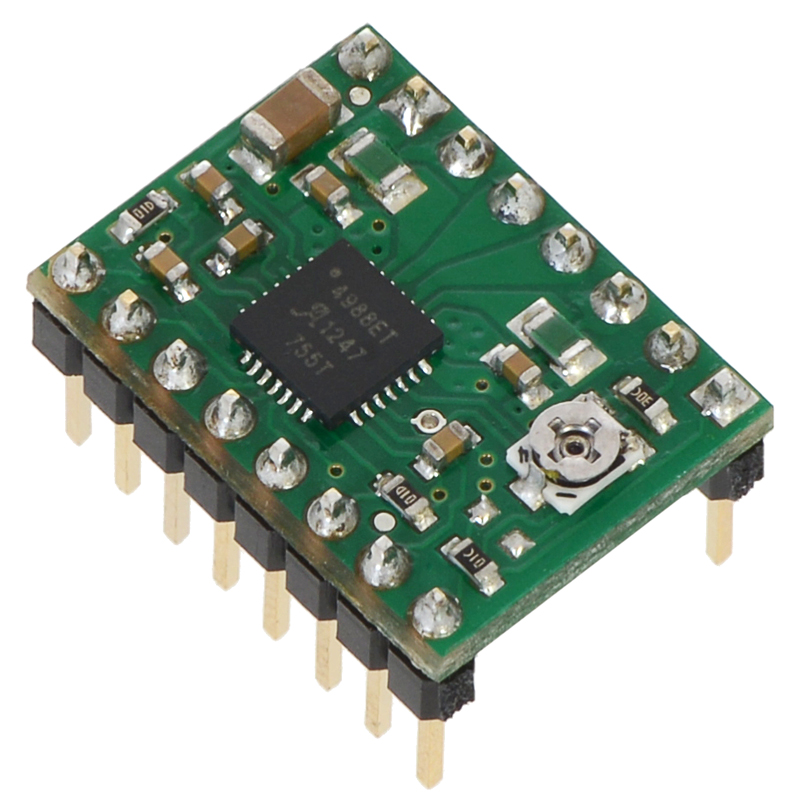
Insufficient torque
For the electronics part everything was first tested separately. The main challenge was of course to combine everything using a PCB and to control everything at the same time with an Arduino. Replacing the potentiometer of the servo to control the opening/closing required some tuning with a real egg. The control of the stepper with the provided required some research and tuning to get a smooth turning using half steps.
When placing the stepper on the structure the stepper did not have enough power/torque to make the platform go up and down. At certain moments the stepper skipped steps (magnetic field was too small compared to the torque that it needed to apply). By turning to the potentiometer on the driver one can control the current that goes to the coils of the stepper and thus the current was tuned in such a way that there was enough torque and the nominal power of the stepper was not exceeded.